What is Porosity in Welding: Important Tips for Getting Flawless Welds
Wiki Article
Porosity in Welding: Identifying Common Issues and Implementing Ideal Practices for Prevention
Porosity in welding is a pervasive issue that frequently goes unnoticed until it creates substantial issues with the honesty of welds. In this conversation, we will certainly discover the crucial variables contributing to porosity formation, examine its detrimental impacts on weld performance, and review the ideal techniques that can be embraced to reduce porosity incident in welding processes.Typical Sources Of Porosity
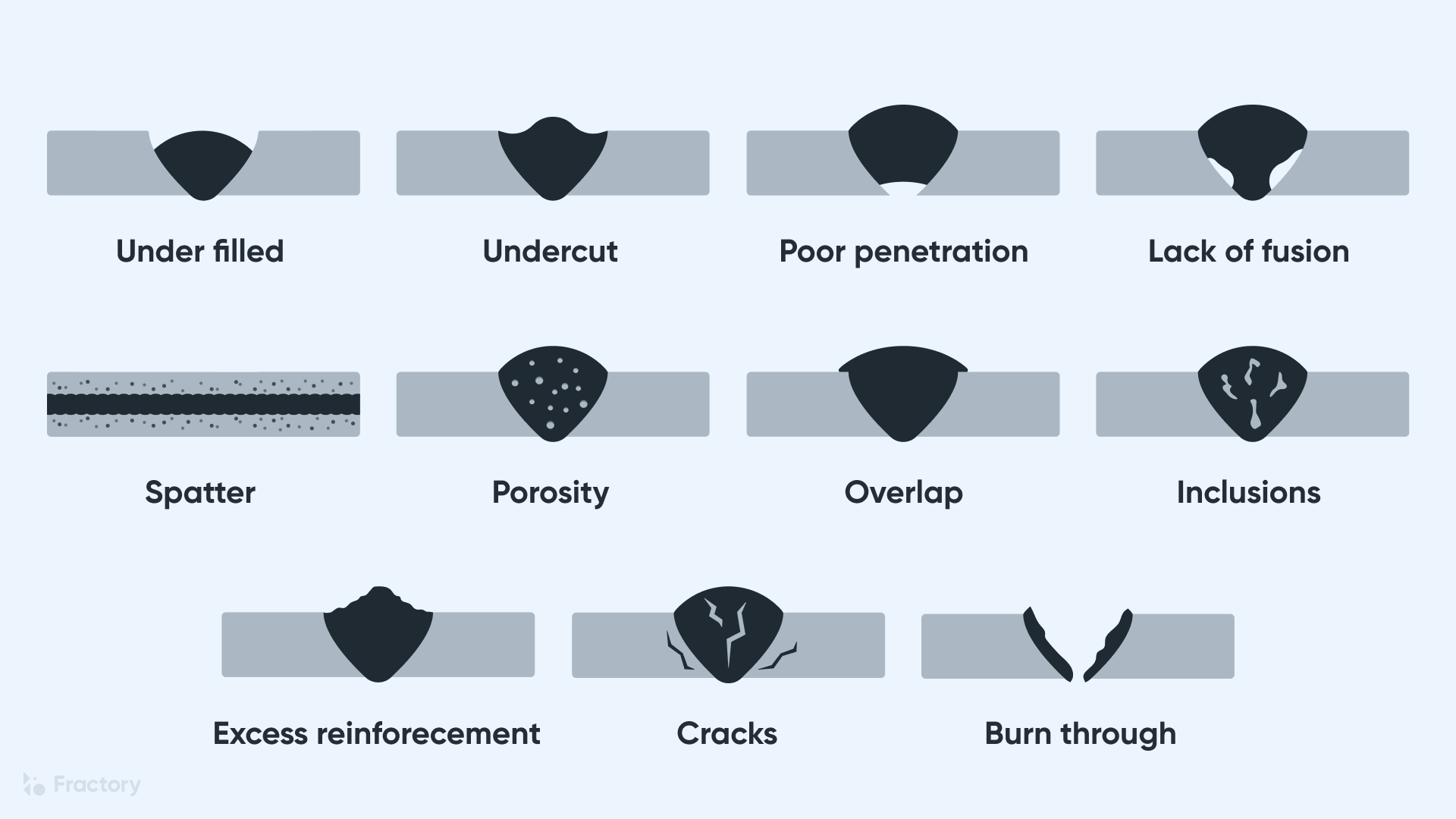
Using dirty or damp filler products can present impurities into the weld, contributing to porosity issues. To minimize these usual reasons of porosity, thorough cleansing of base steels, correct securing gas selection, and adherence to ideal welding specifications are necessary methods in achieving high-quality, porosity-free welds.
Effect of Porosity on Weld Top Quality

The existence of porosity in welding can substantially jeopardize the architectural stability and mechanical properties of welded joints. Porosity creates voids within the weld steel, compromising its general toughness and load-bearing capability.
Among the primary repercussions of porosity is a decrease in the weld's ductility and strength. Welds with high porosity levels have a tendency to show reduced influence strength and lowered capability to deform plastically before fracturing. This can be specifically worrying in applications where the welded components go through dynamic or cyclic loading conditions. Porosity can impede the weld's capability to efficiently transmit pressures, leading to early weld failure and prospective safety and security dangers in vital structures. What is Porosity.
Finest Practices for Porosity Avoidance
To boost the architectural stability and high quality of bonded joints, what specific procedures can be carried out to lessen the occurrence of porosity throughout the welding process? Making use of the proper welding technique for the specific material being welded, such as changing the welding angle and weapon position, can even more protect against porosity. Routine assessment of welds and instant removal of any kind of concerns determined during the welding process are vital practices to stop porosity and create high-grade welds.Importance of Correct Welding Strategies
Applying proper welding methods is vital in making sure the structural integrity and quality of welded joints, developing upon the structure of reliable porosity avoidance procedures. Excessive warm can lead to enhanced porosity due to the entrapment of gases in the weld pool. Additionally, making use of the appropriate welding look at this site criteria, such as you could try these out voltage, existing, and travel speed, is important for attaining audio welds with minimal porosity.Moreover, the option of welding process, whether it be MIG, TIG, or stick welding, should line up with the particular requirements of the job to make certain ideal outcomes. Correct cleansing and preparation of the base steel, as well as selecting the best filler material, are likewise essential components of skilled welding methods. By sticking to these finest techniques, welders can lessen the danger of porosity development and generate high-grade, structurally audio welds.
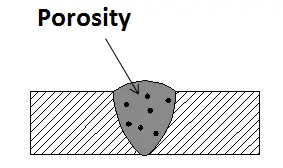
Checking and Quality Assurance Measures
Checking treatments are necessary to identify and protect against porosity in welding, ensuring the strength and resilience of the last product. Non-destructive testing approaches such as ultrasonic testing, radiographic screening, and aesthetic evaluation are frequently utilized to determine potential issues like porosity.Post-weld assessments, on the other hand, analyze the last weld for any type of flaws, including porosity, and validate that it satisfies specified criteria. Applying an extensive top quality control plan that consists of detailed testing treatments and inspections is critical to lowering porosity problems and guaranteeing the overall top quality of bonded joints.
Final Thought
To conclude, porosity in welding can be a typical concern that influences the quality of welds. Web Site By recognizing the typical reasons of porosity and executing finest practices for avoidance, such as proper welding techniques and screening steps, welders can make sure high quality and trustworthy welds. It is essential to focus on avoidance methods to decrease the event of porosity and keep the honesty of welded frameworks.Report this wiki page